Así se construye el Bugatti Chiron, el mejor auto del mundo
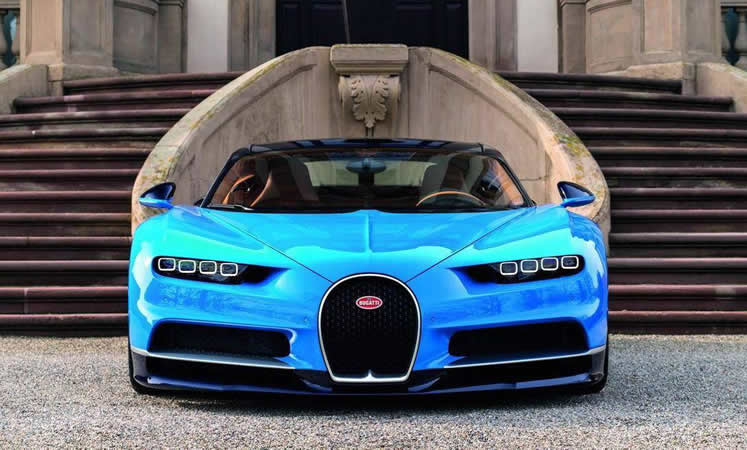
Los primeros modelos del hypercar más codiciado están listos para ser entregados. La compañía de deportivos franceses aprovechó para revelar detalles curiosos de su proceso de fabricación. Cómo se realiza el modelo de calle más rápido de la historia.
Bugatti Chiron nació para romper el tiempo, delimitar un antes y un después en la industria automotriz. Desde su concepción debió soportar la presión de ser el heredero del icónico Veyron. En el Salón del Automóvil de Ginebra 2016 fue presentado en sociedad: el mejor auto de la historia estaba terminado y era real. Su elevada expectativa había sido superada por la fuerza de una obra única. La primera unidad del Chiron está lista para ser entregada. El Grupo Volkswagen, dueño de la marca de deportivos franceses, acompañó este hecho histórico con estadísticas de fabricación que alimentan su espíritu.
El Chiron es una pieza de ingeniería avanzada. Se ufana de cifras estrepitosas y números de vértigo: motor W16 de ocho cilindros que monta cuatro turbos, 1.500 CV de potencia, 1.600 Nm de par máximo, de 0 a 100 kilómetros por hora en 2,5 segundos y 450 kilómetros por hora de velocidad máxima, que fue corroborada en circuitos, sin limitador electrónico de seguridad, en pos de decretar la propiedad del auto más rápido del mundo. Su poder y su prestancia demandan un proceso de fabricación especial.
Se construirán apenas 500 Bugatti Chiron (los primeros 70 se harán en 2017). Será uno de los autos más exclusivos del año. Costará 2,4 millones de euros. Cada unidad precisará de un meticuloso trabajo de fabricación: entre seis y nueve meses, según el grado de personalización ya que un Chiron se construye a mano, de manera artesanal con 1.800 piezas individuales.
Bugatti ofrece una gama de 23 colores exteriores para elegir, más ocho tonalidades que pintarán las franjas de carbono. Se deberán seleccionar otros 31 colores para el interior, 30 para las puntadas y remates de la piel, 18 para las alfombras y 11 para los cinturones de seguridad. Cada pieza se pinta a mano y demanda tres semanas de trabajo: sólo la pintura de la carrocería exterior lleva ocho capas y antes de cada nueva mano, es obligación pulir y lijar la anterior.
En la primera de las doce estaciones de trabajo de la compañía: el motor, un W16 versión reconstruida del Veyron. Viaja desde la Volkswagen en Salzgitter, acusa un peso de 628 kilos, con la certificación de haber superado la prueba de más de ocho horas en un banco que simula todas las exigencias de la caja de cambios de doble embrague y siete velocidades. Durante una semana, tres operarios multitarea integran, montan y ajustan el chasis, el monocasco y los marcos. La parte trasera se construye en torno a su motor: la jungla de cables, tres bombas de agua e inmensas tuberías de enfriamiento precisa de una aplicación más delicada.
Catorce tornillos de titanio -34 gramos de peso cada uno- unen el monocasco y la parte trasera, en uno de los procesos más dramáticos de la construcción del Bugatti. Celebrada esta gesta, se procede a verificar potenciales fugas antes de inaugurar el encendido del motor: durante diez minutos ininterrumpidos se bombea el aceite del motor, el aceite de la transmisión, el líquido de frenos y el fluido hidráulico y refrigerante. Entonces, la magia, el despertar del Chiron, un instante emocionante para el equipo de producción.
Tres horas más para cotejar la función de los bestiales 1.500 CV de potencia. Un dinamómetro – herramienta de medición de fuerza, comprueba la respuesta del deportivo. Luego, cuatro días más para montar las partes más pequeñas y ligeras, para después someter al vehículo a una lluvia de intensidad variable durante media hora con la premisa de garantizar su impermeabilidad. Una vez que el exterior quede sellado, se monta el interior en un proceso de trabajo de tres días. La instalación de un plástico transparente que recubre el interior habilitará la prueba de funcionamiento final.
El examen de aprobación es una experiencia de conducción de 300 kilómetros. Desde la fábrica hasta la pista del aeropuerto de Colmar, cerca de Los Vosgos. Si el piloto de pruebas da su beneplácito, el hypercar regresará a la planta para que le retiren el plástico protector, reemplacen los neumáticos usados por unos nuevos y se someta a seis horas de limpiado y pulido completo. Sólo restará que el proceso de fabricación finalice con la firma de admisión de cada responsable de departamento. El Bugatti Chiron ya estará ansioso por defender en la práctica la profecía del mejor auto del mundo.
Fuente: Infobae